In our previous post on this topic, we looked at the steps to include sustainability in process management. So, what could those steps mean in practice? Let’s take a practical example: improving the company’s warehouse inbound process for raw materials.
But, before that, here are the previously discussed steps as a reminder:
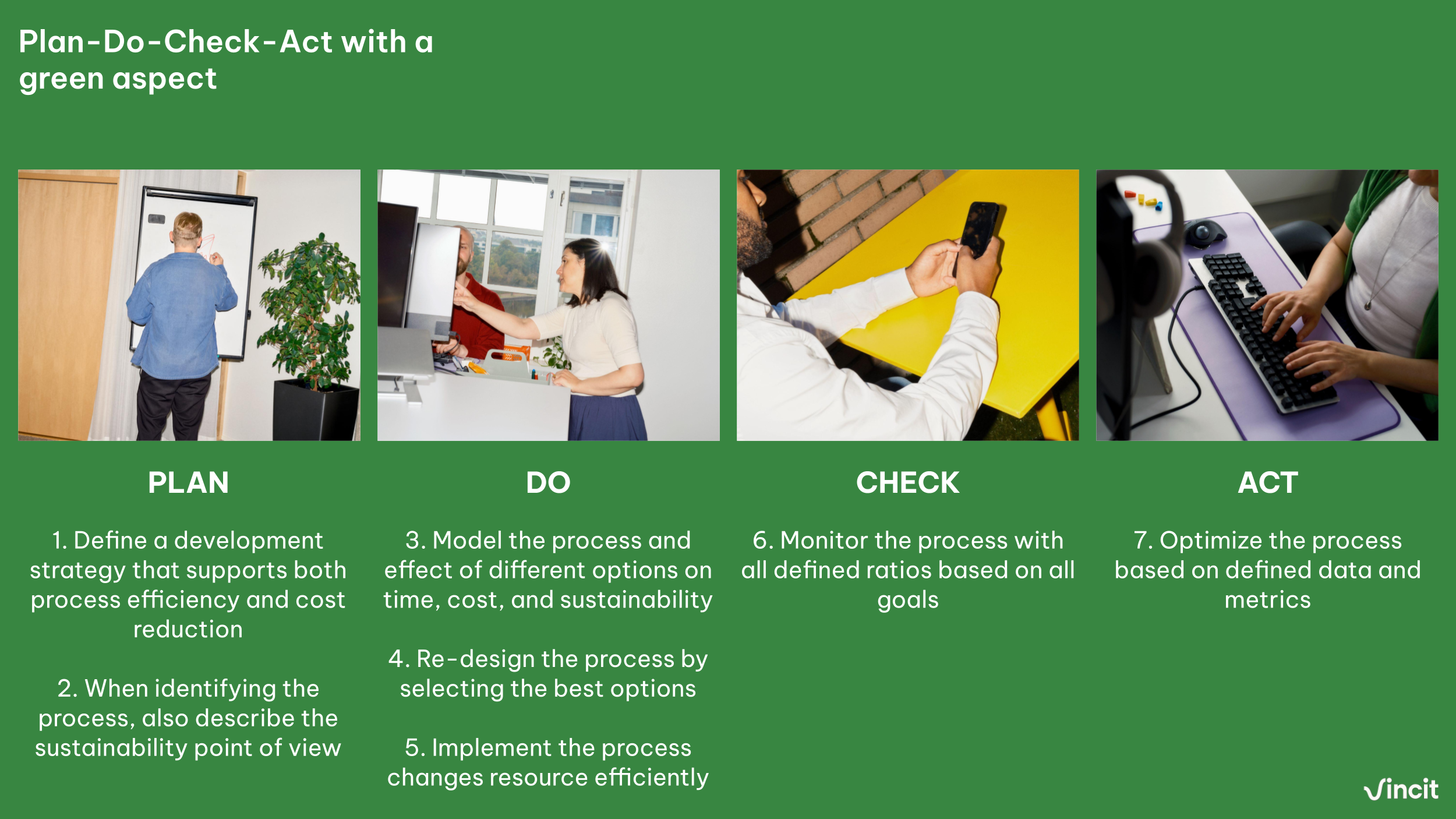
Getting started
The first step is to define the scope and objectives of the business process management initiative. As we incorporate sustainability, we already at this phase include goals and ratios we want to achieve in sustainability in addition to traditional goals. When we describe the process, the following aspects are considered: the scope, boundaries, inputs, outputs, and customers of the process. In practice, describing the process includes:
- Inputs like resource usage (for example electricity, fuel, water, and materials)
- Outputs like waste production and emissions
- Boundaries including legislation, the need to report certain data, and environmental boundaries like requirements that a warehouse must fulfill due to climate, lack of time, lack of resources, lack of sustainability knowledge
Using modern business process management (BPM) software such as SAP Signavio for describing the process can greatly help, but traditional tools can be used as well.
Next, let’s assume that we have BPM software in use where we can efficiently model our process steps and where we can enter some process data to reveal how the current process is working. If we already use a comprehensive enterprise resource planning (ERP) system we can potentially even use process mining to see how the process varies and where process performance is at the moment. This of course means that we have in the first BPM phase – goal setting – been able to define the process performance indicators that will be derived from the process data. In case our green strategy is still on a very high level or we do the process work for the first time, then we first need to describe the process and after that use some time to derive tangible ratios to include to do a performance estimation for that process.
Next, let’s assume that we have BPM software in use where we can efficiently model our process steps and where we can enter some process data to reveal how the current process is working. If we already use a comprehensive enterprise resource planning (ERP) system we can potentially even use process mining to see how the process varies and where process performance is at the moment. This of course means that we have in the first BPM phase – goal setting – been able to define the process performance indicators that will be derived from the process data. In case our green strategy is still on a very high level or we do the process work for the first time, then we first need to describe the process and after that use some time to derive tangible ratios to include to do a performance estimation for that process.
Including sustainability to process improvements
In the modeling phase, for each stage in the process, we need to define which factors are relevant from a performance improvement point of view – traditionally we estimate time and cost. Now we need to estimate sustainability as well. We include sustainability often through resources used and possible waste and emissions produced during each process stage. But sustainability can include other aspects as well depending on the process in question.
Mostly the sustainability goals align well with other process goals but sometimes they’re conflicting. In our example, inbound warehouse process factors will most likely include devices and time/energy needed to unload and move the raw materials, the type and amount of warehouse space needed while storing the material, waste from the packages, and the possibility of recycling. We can even decide to attach sensors to raw materials in the inbound process to ensure that material is stored appropriately and limit unnecessary costs and waste. Sensors in turn require some energy, a network, and data storage, so we need to ensure that savings are larger than additional cost and resource consumption.
After defining and modeling the process we’re working with, we need to consider the ways this process can be improved – for example by cost, time, and resources spent as well as from a waste/emission reduction point of view. At the same time, the process needs to meet the legal requirements for this type of process. If process work isn’t at an advanced level in the company, it’s often useful to first concentrate on just standardizing the process and removing unnecessary variations.
Mostly the sustainability goals align well with other process goals but sometimes they’re conflicting. In our example, inbound warehouse process factors will most likely include devices and time/energy needed to unload and move the raw materials, the type and amount of warehouse space needed while storing the material, waste from the packages, and the possibility of recycling. We can even decide to attach sensors to raw materials in the inbound process to ensure that material is stored appropriately and limit unnecessary costs and waste. Sensors in turn require some energy, a network, and data storage, so we need to ensure that savings are larger than additional cost and resource consumption.
After defining and modeling the process we’re working with, we need to consider the ways this process can be improved – for example by cost, time, and resources spent as well as from a waste/emission reduction point of view. At the same time, the process needs to meet the legal requirements for this type of process. If process work isn’t at an advanced level in the company, it’s often useful to first concentrate on just standardizing the process and removing unnecessary variations.
Using a modern ERP
For a smaller company, a valid approach could be a modern ERP system that offers directly standardized industry best practice processes to start with (like SAP Public Cloud). If a company already uses a modern ERP system, we can additionally check suggestions our possible BPM software gives us based on our current data. Whatever way we collect improvement possibilities, it’s highly important to estimate the potential together with sustainability and process experts to ensure that options are selected wisely.
In the implementation phase, we select the ratios we aim to improve and work together with all process experts and shareholders involved in the process steps to implement the changes incrementally to achieve a more sustainable and efficient process. The first changes are always made without full knowledge of their effect. Data collection and analysis of process change, as well as process optimization, come into the picture directly after implementing the first changes.
This blog aimed to highlight the advantages of combining sustainability with a company's regular process improvements. In the next blog in this series, we’ll examine the data and tools needed to implement and report sustainability more closely.
In the implementation phase, we select the ratios we aim to improve and work together with all process experts and shareholders involved in the process steps to implement the changes incrementally to achieve a more sustainable and efficient process. The first changes are always made without full knowledge of their effect. Data collection and analysis of process change, as well as process optimization, come into the picture directly after implementing the first changes.
This blog aimed to highlight the advantages of combining sustainability with a company's regular process improvements. In the next blog in this series, we’ll examine the data and tools needed to implement and report sustainability more closely.
Contact Sari Mikkonen to learn more about how SAP Public Cloud can create a solid foundation for improving your business processes and sustainability: sari.mikkonen@vincit.com
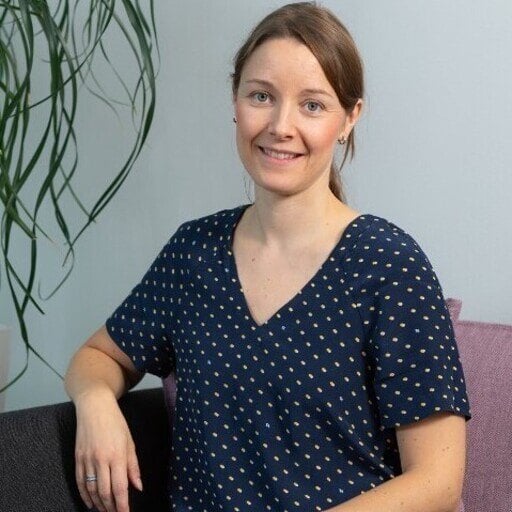
Marika Okko,
Managing Consultant